Tam ve çeşitli disk granülasyon üretim hattı süreci, Henan Zheng Heavy Industries'in ana avantajlarından biridir.Müşterilerin gerçek ihtiyaçlarına göre eksiksiz ve güvenilir üretim hattı çözümleri sunabilmektedir.
Çeşitli gübre üretim hatlarının planlanması ve servisinde deneyime sahibiz.Sadece üretim sürecindeki her süreç bağlantısına odaklanmakla kalmıyoruz, aynı zamanda tüm üretim hattındaki her sürecin ayrıntılarını her zaman yakalıyor ve başarılı bir şekilde birbirine bağlanmayı sağlıyoruz.
Disk granülatörün üretim hattı esas olarak organik gübre üretmek için kullanılır.Organik gübre, hayvan ve kümes hayvanı gübresi, tarımsal atıklar ve belediye katı atıklarından yapılabilir.Bu organik atıkların, satışa yönelik ticari değeri olan ticari organik gübrelere dönüştürülmeden önce daha fazla işlenmesi gerekmektedir.Atığı zenginliğe dönüştürmeye yönelik yatırım kesinlikle değerlidir.
Disk granül organik gübre üretim hattı aşağıdakiler için uygundur:
- ►Sığır gübresi organik gübre imalatı
- ►Domuz gübresi organik gübre imalatı
- ►Tavuk ve ördek gübresi organik gübre imalatı
- ►Koyun gübresi organik gübre üretimi
- ►Kentsel çamurun organik gübre üretimi
1. hayvan gübresi: tavuk gübresi, domuz gübresi, koyun gübresi, inek gübresi, at gübresi, tavşan gübresi vb.
2. endüstriyel atıklar: üzüm, sirke cürufu, manyok artığı, şeker artığı, biyogaz atığı, kürk artığı vb.
3. Tarımsal atıklar: mahsul samanı, soya fasulyesi unu, pamuk tohumu tozu vb.
4. Evsel atık: mutfak çöpü
5. çamur: kentsel çamur, nehir çamuru, filtre çamuru vb.
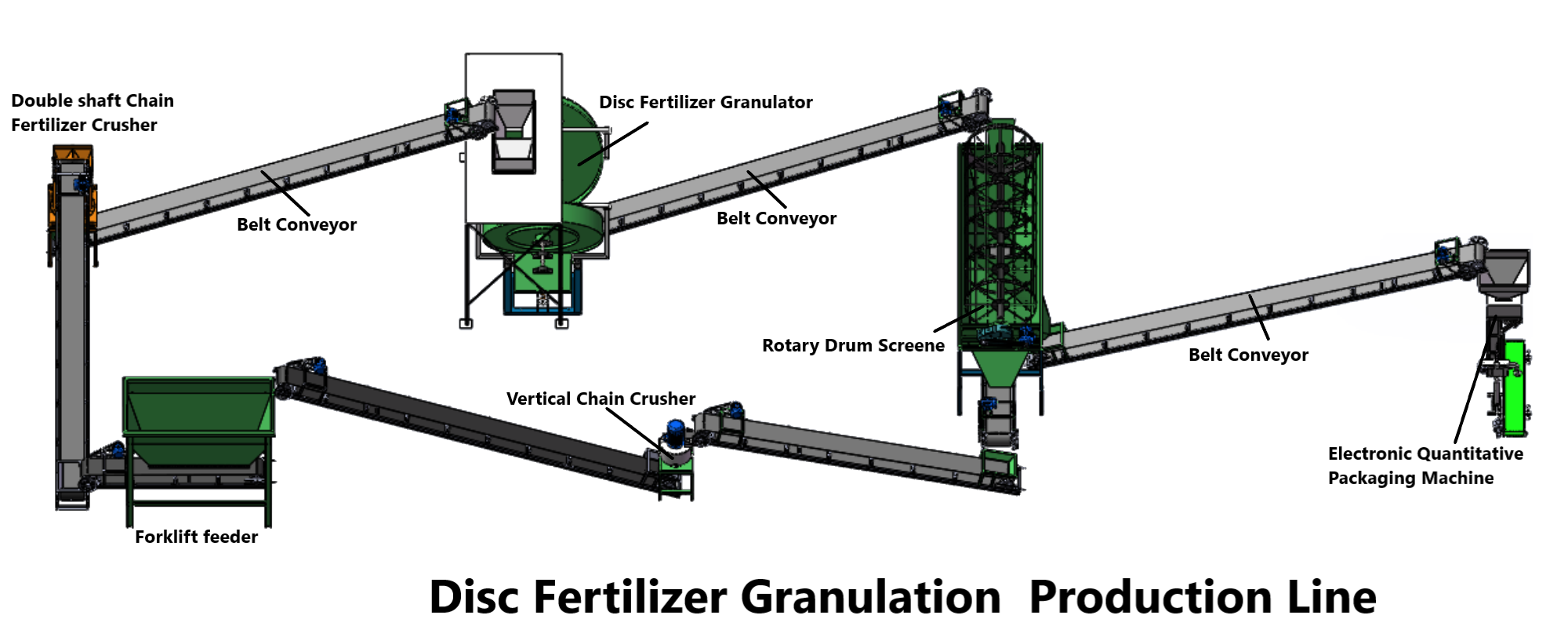
Disk granülasyon üretim hattı gelişmiş, verimli ve pratiktir, ekipman yapısı kompakttır, otomasyonu yüksektir ve işlemi basittir, bu da organik gübrenin seri üretimi için uygundur.
1. Tüm üretim hattı ekipmanlarında korozyona ve aşınmaya dayanıklı malzemeler kullanılmaktadır.Üç atık emisyonu yok, enerji tasarrufu ve çevre koruma.Sürekli çalışır ve bakımı kolaydır.
2. Üretim kapasitesi müşteri ihtiyaçlarına göre ayarlanabilir.Tüm üretim hattının düzeni kompakt, bilimsel ve makuldür ve teknoloji ileri düzeydedir.
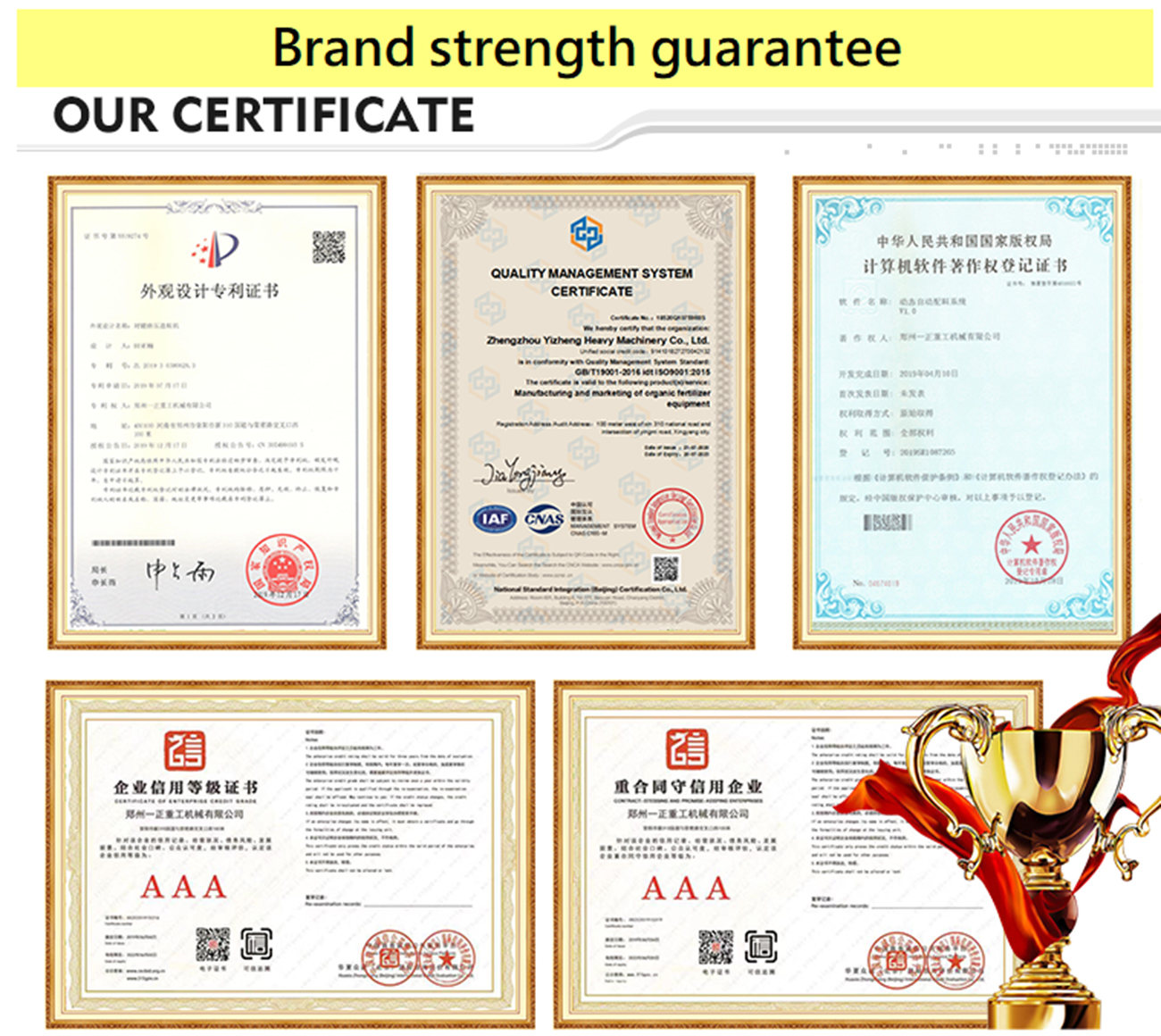
Disk granülasyon üretim hattı ekipmanı, malzeme deposu → blender (sırma) → disk granülasyon makinesi (granülatör) → silindirli elek makinesi (standart altı ürünleri bitmiş ürünlerden ayıran) → dikey zincirli kırıcı (kırma) → otomatik paketleme makinesi (paketleme) → bantlı konveyör ( çeşitli süreçlere bağlanma).
Not: Bu üretim hattı yalnızca referans amaçlıdır.
Disk granülasyon üretim hattının proses akışı genellikle aşağıdakilere ayrılabilir:
1. Hammadde içerikleri süreci
Sıkı hammadde oranı yüksek gübre verimliliği sağlayabilir.Hammaddeler arasında hayvan dışkısı, çürük meyveler, kabuklar, çiğ sebzeler, yeşil gübre, deniz gübresi, çiftlik gübresi, üç atık, mikroorganizmalar ve diğer organik atık hammaddeleri bulunmaktadır.
2. Hammadde karıştırma işlemi
Tüm hammaddeler karıştırıcıda eşit şekilde karıştırılır ve karıştırılır.
3. Bozuk süreç
Dikey zincirli kırıcı, büyük malzeme parçalarını granülasyon gereksinimlerini karşılayabilecek küçük parçalara kırar.Daha sonra bantlı konveyör malzemeyi disk granülasyon makinesine gönderir.
4. Granülasyon süreci
Disk granülasyon makinesinin disk açısı yay yapısını benimser ve bilya oluşturma oranı %93'ün üzerine çıkabilir.Malzeme granülasyon plakasına girdikten sonra, granülasyon diskinin ve püskürtme cihazının sürekli dönüşü yoluyla, malzeme düzgün bir şekle ve güzel bir şekle sahip parçacıklar üretmek için eşit şekilde birbirine bağlanır.
5. Tarama süreci
Soğuyan malzeme elemek üzere valsli elek makinesine taşınır.Nitelikli ürünler bitmiş depoya bantlı konveyör aracılığıyla girebilir ve ayrıca doğrudan paketlenebilir.Niteliksiz parçacıklar yeniden tanelenmek üzere geri dönecektir.
6. Paketleme süreci
Paketleme organik gübre üretim hattının son işlemidir.Bitmiş ürün tam otomatik kantitatif paketleme makinesiyle paketlenir.Yüksek derecede otomasyon ve yüksek verimlilik, yalnızca doğru tartım sağlamakla kalmaz, aynı zamanda son prosesi de mükemmel şekilde tamamlar.Kullanıcılar besleme hızını kontrol edebilir ve hız parametrelerini gerçek gereksinimlere göre ayarlayabilir.